It's been nearly a month since my last blog. I have been researching a makeover for the Probatron. I am going for a bright metallic red with gold flip accent effect and a nice set of Ace C036 turbofan wheels (with 215-35-18 tyres) as painted alloys. I wanted the chrome ones, but I have been put off because chrome alloys have a tendency to peel and then pit if the car is not kept in a garage and only brought out in nice weather, but painted alloys are much more resilient to the weather. I am not sure what is going to happen about the trims for the front, rear and side quarter windows as I am being told that new ones only come with the glass. It needs new trims, but may also need new glass throughout and this would add considerable cost to the makeover. If this is what is needed then it shall be done. I don't want to have new paint with scruffy window trims as this will spoil the overall effect.
I have clocked over 4000 electric miles now. Since I last fixed the throttle, I have had no further issues apart from reduced range affecting the batteries in this the cold weather.
It was heavy snow last night and I went to work in it today. I had to be really careful, because unlike a petrol car, I have uncontrolled torque and lots of it at low revs and that means wheel spin and lots of it. I kept having to back off the throttle to stop the wheel spin, but I was not developing much forward speed to get me on my way. Using great skill I made it to work and then the journey home was even worse as the ice had been polished by a whole days traffic. My journey to work is normally exactly 7 miles, but today it was 7.4 that means I had wheel spun for 0.4 miles in that short journey. Fortunately I can work from home and I shall if it is the same tomorrow. One good point though, there were no issues with the car itself.
171: Friday 5th November 2010
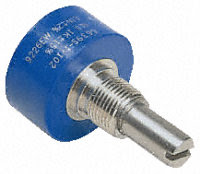
I had ordered a conductive plastic precision potentiometer and it came yesterday. I got a 5k pot this time as I could not find a 10k precision conductive plastic one. The Manual for my controller states that the pot needs to be between 500R and 10k, so this one is fine. I changed it over on the pot box even though the cheap carbon track pot with the thin plastic shaft was still working o.k. The difference is that there is almost no friction on the conductive plastic track, the linearity of the track is much better than a carbon track, the metal shaft supports the spring and throttle arm with no issues. Another thing I noticed was how easily the shaft of the pot turned. The wire wound types that I had were very stiff. This new pot was extremely smooth and easy, but feels really solid. It cost me £17 by the time it was posted to me and taxed etc. This is double what I paid for the last wire wound pots that I bought. These are now consigned to the reserves bench even though they have never been used. Hopefully my throttle problem is permanently solved, or at least for a very long time (years???).
170: Tuesday 3rd November 2010
Nightmare, it happened again! Another potentiometer bites the dust again. It is a good job I have a bag full of cheap pots in my garage, so I transplanted another of these small 10k pots onto the control box with my special brass shaft adapter. I have a feeling that the spring is causing these pots to break down as it is bending the shaft a bit when the throttle is planted. Also the microswitch for the throttle decide to come apart and the bits fell on the floor. I managed to find them all and re-assemble it. When I broke down I put into effect my contingency plan to insert a resistor into the connector for the pot, but in the process I accidentally pulled out some control wires. It took me a little while to notice this and in the process of doubting the correctness of my resistor connection, I pulled one of the pot wires out of the connector. I only had about 1 mile to go, so I fixed the wires in place as best as I could, then got the motor running after a fashion. Unfortunately I could not get enough power to get moving, so I set the creep speed up to maximum and used a back route down a side street that was very quiet and crept along the road. I went over a bump and suddenly I had some on/off acceleration just as I was about to rejoin the main road, cool. I jerked it home (it wasn't too bad in 3rd gear) and parked up. After fitting the cheap pot all is back to normal and the throttle response is smooth again. I know I have 2 heavy duty wire wound pots waiting to be picked up from the post office tomorrow, and I have now ordered a conductive plastic 1w pot as one of my colleagues suggested this might be a better choice. Wire wound pots seem to be useless. I am still looking out for a hall effect sensor that is suitable as well. Hopefully the conductive plastic pot will work out. If it starts getting rough then I will go for a hall effect rotary sensor.
169: Thursday 28th October 2010
I had a chat with some of the guys at work about the throttle pot and I am going to see if I can track down a hall effect throttle positions sensor. I know I can get an automotive potentiometer and this will do to get started. Hopefully we can find something tomorrow or I will have to buy another unproven pot. The one I fitted yesterday is still o.k. at the moment. I am starting a guide to converting a car to electric on another blog. I shall put the address in the next posting. If you have any burning question, I will answer them in that blog. I shall keep this blog for the Probatron and the different experiences I have with him.
and here it is:
http://www.ev-convert.blogspot.com
and here it is:
http://www.ev-convert.blogspot.com
168: Wednesday 27th October 2010
Another one bites the dust. I broke down again today, I lost throttle control completely. The controller programmer box was indicating the accelerator voltage fault. Double disaster, my mobile phone battery had gone flat and I put it on charge through my USB port at work, and left it there. So here I was half way up a busy hill, hazard lights on, no drive and no phone. As all the angry drivers overtook me, I gradually backed up to a side turning and with a bit of a run up (backwards) I managed to go round the corner and get parked rather well in one move. I think it was more luck than judgement. I locked up the Probatron and went off to the nearby shops to find a payphone. Fortunately my wife had just come in and answered the phone. I got her to bring some 10mm spanners so I could remove the throttle and take it home for repair. She stayed with sparky while I went home and changed the pot. About an hour after the first phone call I was back on the road again on the way home. I am having a run of bad luck with potentiometers. However, I have found that the original pot that was too high for my controller at 20k ohms had a 10k resistor in parallel to bring it down to below 10k. Closer examination found that when this started playing up it was only the 10k resistor on the pot that kept it going, other wise it would have failed just like this one. This leads me to a quick repair that I can do so I don't get stranded in future. I shall keep a 10k resistor in the car and if my throttle fails again, then can links this across the input so the voltage can be detected even if it is wrong, it may be jerky, but it will get me home and the throttle switch safety override will prevent any run away as drive is removed when I lift off the pedal (and hence the micro switch). It's not perfect, but until I find a better throttle potentiometer it will get me home. I did find one on eBay that looks exactly like the original, but I can get it as a 10k linear pot, cool.
167: Monday 25th October 2010
I travelled one mile this morning and turned back home. My temporary throttle had given up and I could only muster 20 mph. I came back home told my beloved that I was going to take her car to work, she told me otherwise, then a few minutes later after a short discussion I was out in the garage very hurriedly fixing my car with another temporary potentiometer. It actually only took me about 20 minutes to fix it. I got to work o.k. and home again, but it was being a bit tetchy on the way home too. Fortunately my new throttle potentiometers came in the post today. In the photo below you can see 3 pots. Sorry about the picture quality as my digital camera had run out of batteries. I put some new ones in and they died straight away. I need to get some better batteries, so I had to use my phone instead. Anyway, the big pot is the original that came with the metal box and lever, the little one is what I have used for a temporary fix, and the orange / red one is the new one. The temporary pot has a 4mm plastic shaft. The new pot has the right size shaft and it is metal. I rewired my state of charge gauge too, so now it represents the voltage levels at all times, but I wired it to the wrong side of my throttle switch, so the gauge only reads when I press the throttle. It will be a quick fix tomorrow. The throttle response is superb now. Previously I had to press the throttle pedal about half way before I got forward drive. It did not seem to matter how I calibrated it. I can only assume the pot track was laid like that. As this new pot is wire wound, it accelerates as soon as I touch the throttle and feels just like the throttle pedal on a petrol car. It is smooth and really nice to drive. I don't feel like I have to drive it special now. I am really pleased with this.
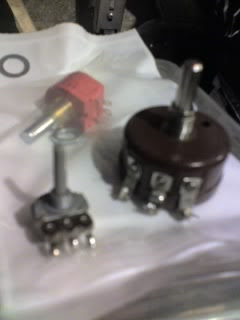
166: Saturday 23rd October 2010
It has happened again, but this time I can detect the symptoms. The throttle pot is starting to go again, so I have limited my car use over the weekend as I have some new pots on order. 10k 1W wire wound linear pot x 2 should hopefully do the job and I have a spare in case they are not quite up to the job. There are higher wattage types also, but I believe the ones I have fitted now cannot tolerate being outdoors and being a carbon track type, it would not behave well with moisture. The wire wound type is sealed and much more tolerant of moisture. Hopefully this will be something I can put to bed for some time. The new pots should arrive Monday and will probably take about an hour to fit.
165: Sunday 17th October 2010
Today I was dropping off a friend of my daughter, then I lost control of the throttle. I was getting no drive until I nailed the throttle pedal, then I got full throttle. It was like having a throttle switch with full on and full off as the only states. I put him in 3rd gear to smooth the drive out a bit and got home. I checked the throttle using the tester function on the controller with the gearbox in neutral and I could see no change until about 80% when the motor fired up. So the throttle potentiometer was playing up. This a heavy duty sealed type potentiometer, so there was nothing I could do but change it. I had some 10k pots in my electronics spares, but the shaft was 4mm compared to 8mm of the original, so I used some brass tubing to increase the shaft size. I fitted the lever back and put it all on the car, then I had the controller learn the new throttle pot extremes. When I tried it again, control was back to normal so I had nice control across the range of the pedal. Thankfully this happened in the early afternoon, so I had a good amount of time to solve the problem. So it all seems o.k. now and I have a bag full of these potentiometers in my garage in case it goes again. I think this was my first breakdown where something has actually gone wrong and needed repair other than just charging up. I am not counting my original batteries as they were second hand to start with and only a temporary solution. When they did give in, it was nothing less than expected and planned for.
164: Saturday 16th October 2010
I knew it was a mistake to say that Sparky was behaving himself. The Probatron was all charged ready for its first trip to football training. We set out with 18 miles done, arrived at the normal time at football training with 125v still reading on the tester, all was well. 2 hours later we set off to come home and once we were on the main road it seemed to be constantly uphill all the way home. I was watching the battery voltage going down and down until when we was about 6 miles from home the controller started cutting out. I limped it into a lay by and just let the voltage build up again. when we were back at 120v I set off again, but I knew it wouldn't last long. We got within 2 miles of home and it was cutting out again. I knew we had a hill to go up, so we stopped for another 5 minutes or so to let the voltage recover again, and we managed to limp home. After about 4 hours of charging a quick local trip out and all was back to normal. It is clear now that the Probatron cannot maintain a long period of higher current. I could probably try again using up to 3rd gear only so as to keep the current lower and drive at a slower speed, say 50 mph. I also believe that having my daughter and my wife probably added over 100kg of weight and this affected the range. So for now I shall set a 30 mile limit for our journeys when we are all in the car as we got to 31 miles when it cut out first time today. I just hope this hasn't affected the life of the batteries too much. I can't believe my test runs gave me 40 miles with maybe a couple more to spare. However this was done in several shorter journeys. I learnt something today. It is good to know the Probatron is back to normal just for a charge though.
163: Friday 15th October 2010
Nothing much happening with the Probatron recently. It has been behaving itself.
----
There has been, and will continue to be an accelerated amount of news surrounding the introduction of the various large brand offerings of electric cars.
----
The Chevy Volt has taken a beating in the press for keeping some of the details about the drive system quiet while they get their patents sorted out. Nissan are soaking up all the press they can get for their battery only electric vehicle the Leaf. Mitsubishi with the iMiev battery car, Peugeot's ion (iMiev with different calibrations and paint job), the Renault Fluence and the relationship with Better Place for battery swapping stations etc.
----
I am confident we will start seeing lots of pretentious adverts on TV soon, if they haven't already started. I have seen some on-line. My wife loves the Nissan Leaf polar bear advert, but was only interested in how cuddly the bear was, no interest in the car at all.
----
There has been much talk about how China wants to control the technology that is allowed to be sold there.
----
As you may know I work for Ford, and initially they had others build retro-fit prototypes in the form of Smiths for the Transit Connect and Magna for the Ford Focus and then taken them on to develop it further in the Ford factories. The Transit connect now being kitted out by Azure Dynamics and the Focus still by Magna. Fairly well proven systems in both cases and Ford are not making so much noise about the electrification as some of the other brands and in my opinion appear to be offering the customer electric options if they want them rather than thrusting a position or standpoint on the public. There has been some publicity, but not too much boasting.
----
Then to continue my rant, there is all the hoo-har about charging points. I know that in the U.K. I could plug in just about anywhere there is a 240v 3 pin plug. It seems that every utility company has a fancy looking post with a socket on it that costs thousands of $s or £s. It cost me less than £20 to set up a 240v 16A socket alongside my garage door. I find it frustrating that the authorities can't just find a local electrician to put in 10 ordinary electric points that are suitable for car charging in every large car park and pay the car wash guy to paint them spaces green with some floor paint and write "Electric Car Parking" alongside all for about £2000. That would be about 2 days work for me on my own and would make me fairly well-off if I could get a couple of gigs each week. Apart from everything else it could all be done in just a few months and cost just a few millions for the whole country. It seems that we are seeing this sort of money being spent just on consultations with not a damn thing being installed anywhere. Then when some fancy posts do appear one or two at-a-time in some obscure places and then cost 10s of thousands of pounds or dollars.
----
I read regularly about people arguing that coal fired power stations producing CO2 when generating electric that would be used to charge cars. No matter who does the calculating, this still pollutes less than the millions of petrol cars on the road, but the figures now show that truly electric cars are not completely clean. I watched a program on TV that had the American government in for about 1.5 trillion dollars worth of coal fired power stations before 2050 with a life expectancy of about 50 years, but using sequestration to clean the emissions into porous rock beds. I am not totally convinced that this egg basket is the right place to put all your solutions either. So another idea to come out was closed nuclear power stations where the waste is re-used over and over. Wind power and solar power don't have enough coverage for the outlay to provide for all.
----
For all the things that are starting now, the next 5 years are going to be really interesting. I would be surprised if there was another war somehow related to the introduction of electric cars and at least one major environmental disaster. I am sure that in 2015 we will still be trying to understand what is the winning solution set, whether this is right or wrong, and by 2020 we will be wondering what all the fuss was about.
----
I will be really interested to get some comments going on these subjects since I have only got my amp gauge and matrix display to build now for the Probatron. Plus adding Lambo door hinges and a blingy paint job.
----
There has been, and will continue to be an accelerated amount of news surrounding the introduction of the various large brand offerings of electric cars.
----
The Chevy Volt has taken a beating in the press for keeping some of the details about the drive system quiet while they get their patents sorted out. Nissan are soaking up all the press they can get for their battery only electric vehicle the Leaf. Mitsubishi with the iMiev battery car, Peugeot's ion (iMiev with different calibrations and paint job), the Renault Fluence and the relationship with Better Place for battery swapping stations etc.
----
I am confident we will start seeing lots of pretentious adverts on TV soon, if they haven't already started. I have seen some on-line. My wife loves the Nissan Leaf polar bear advert, but was only interested in how cuddly the bear was, no interest in the car at all.
----
There has been much talk about how China wants to control the technology that is allowed to be sold there.
----
As you may know I work for Ford, and initially they had others build retro-fit prototypes in the form of Smiths for the Transit Connect and Magna for the Ford Focus and then taken them on to develop it further in the Ford factories. The Transit connect now being kitted out by Azure Dynamics and the Focus still by Magna. Fairly well proven systems in both cases and Ford are not making so much noise about the electrification as some of the other brands and in my opinion appear to be offering the customer electric options if they want them rather than thrusting a position or standpoint on the public. There has been some publicity, but not too much boasting.
----
Then to continue my rant, there is all the hoo-har about charging points. I know that in the U.K. I could plug in just about anywhere there is a 240v 3 pin plug. It seems that every utility company has a fancy looking post with a socket on it that costs thousands of $s or £s. It cost me less than £20 to set up a 240v 16A socket alongside my garage door. I find it frustrating that the authorities can't just find a local electrician to put in 10 ordinary electric points that are suitable for car charging in every large car park and pay the car wash guy to paint them spaces green with some floor paint and write "Electric Car Parking" alongside all for about £2000. That would be about 2 days work for me on my own and would make me fairly well-off if I could get a couple of gigs each week. Apart from everything else it could all be done in just a few months and cost just a few millions for the whole country. It seems that we are seeing this sort of money being spent just on consultations with not a damn thing being installed anywhere. Then when some fancy posts do appear one or two at-a-time in some obscure places and then cost 10s of thousands of pounds or dollars.
----
I read regularly about people arguing that coal fired power stations producing CO2 when generating electric that would be used to charge cars. No matter who does the calculating, this still pollutes less than the millions of petrol cars on the road, but the figures now show that truly electric cars are not completely clean. I watched a program on TV that had the American government in for about 1.5 trillion dollars worth of coal fired power stations before 2050 with a life expectancy of about 50 years, but using sequestration to clean the emissions into porous rock beds. I am not totally convinced that this egg basket is the right place to put all your solutions either. So another idea to come out was closed nuclear power stations where the waste is re-used over and over. Wind power and solar power don't have enough coverage for the outlay to provide for all.
----
For all the things that are starting now, the next 5 years are going to be really interesting. I would be surprised if there was another war somehow related to the introduction of electric cars and at least one major environmental disaster. I am sure that in 2015 we will still be trying to understand what is the winning solution set, whether this is right or wrong, and by 2020 we will be wondering what all the fuss was about.
----
I will be really interested to get some comments going on these subjects since I have only got my amp gauge and matrix display to build now for the Probatron. Plus adding Lambo door hinges and a blingy paint job.
162: Wednesday 29th September 2010
Yesterday I did another range check run. I drove carefully home from work using the gears to try and keep the motor in its most efficient ranges. I got a phone call to pick up my daughter from school, then I dropped her off to her friends later. So I headed for the main road and had clocked 10 miles before I started my run. My objective was to achieve at least 36 miles so I could do the return journey to football training every Saturday and when we have a home match on Sundays. Our Jeep Cherokee is only returning 13mpg round the streets and not much better on a run, so this will save us another £60 per month by my reckoning. Anyway back to the range run, I hit some traffic and that slowed me down, but I managed to keep going at a steady rate and got home with 116v and 40miles on the clock, perfect. I am sure that starting from home and going to football that is a continuous run the whole time is easily possible and I shall do it first time this weekend. Today I was going along the very last stretch of road at work before the car park and I got a real bad squealing from the right rear wheel when braking. It was really loud. I had no choice but to drive home like this as it did not affect the driving. I got the car up on a jack and checked the wheel and found that the anti squeal bracket had somehow got pushed across and was causing the squeal by rubbing on the brake disc. For this to happen, the brake pads would need to have opened wide and then one of them got caught on the edge of the squeal plate to push it across when the brake was applied. I cannot figure out how this happened. I took 2 screwdrivers and manipulated the squeal plate back in position and all is well again. I also fitted some locking wheel nuts that I have had for some time now. I had one rusty plain wheel nut on each wheel as the last lot of locking nuts broke and rusted. So all nice shiny nuts now :-) and 40 miles range.
161: Tuesday 28th September 2010
Last night I went for a run along the main road near where I live to get a better idea of my range with these new batteries. I had already come home from work (7 miles) in sport mode without much regard for economising. I then dropped my daughter off at her friends house and started my run with about 9 miles already done. I completed 34 miles and ran the batteries down to 115.2 volts which is a bit further than I wanted to go. The car was still driving fine when I pulled up at home with hardly any noticeable loss of acceleration or speed. I did the whole distance in sport mode, so on several occasions I would have been drawing 800A. I also completed the whole run in 3rd gear including pulling away and cruising at 55 to 60 MPH. I hope to do another trial tonight from when I leave work with a full charge, I will drive in economy mode and use the gears for pulling away and above 40 mph I shall use 4th and 5th gear in order to maximize regen braking. I still could do with setting my brushes to a neutral position as they are currently set advanced for CCW operation. This is not ideal for regen braking and causes arcing above approximately 3500 rpm. However I can go up to 57 MPH in 4th gear at 3500 rpm, so I should not need to go above 4th to get max regen without arcing. Also 4th gear should be able to take me to 80 MPH at about 5000rpm. In economy mode the current will be limited to 500A, so this should also increase the range a bit.
160: Monday 27th September 2010
I have now completed over 3000 miles of electric driving since 9th March 2010. After fixing the problem of the batteries shifting from side to side I am now getting a banging noise from the bracket when I go over big bumps in the road. I know I don't have much suspension travel with all the batteries in the trunk, but this is not the problem. When I mounted the battery rack I used riv-nuts just to hold the rack in place and to stop movement from side to side and back and forth. The problem is none of these things, but the batteries are trying to jump up when I go over a big bump and I believe this has pulled the riv-nuts out. They will still keep the rack in position, but not for jumping up on bumps. Fortunately the holes for the riv nuts are easily accessible from under the car, so I should be able to re-fix the bracket with bigger bolts and using nuts and big washers underneath. This should hold the bracket down and get rid of the banging noises. I never really had this problem with the old batteries, so I need to spend a bit of time just shoring these up some more. I may find some time this week to work on the instruments some more too.
159: Sunday 19th September 2010
I tightened the nuts on the hold down brackets in the trunk, and checked the connections. All is still well. I am coming up on 3000 electric miles recorded. You may remember that my speedo was broken for a while when there was some plastic fragments jammed in the mile counter, so I have probably already passed this point now, but I have about 100 miles to go before it shows on my clocks. I have been busy rebuilding my kitchen so I have not done much to the Probatron for a while now. I hope to start publishing some more detailed accounts of certain parts of the build. I tend to provide just enough information to make it readable by most people, so if you have a suggestion of a part of my build you want explained in more detail then please leave a comment and we can have some dialogue before I publish a detailed account.
158: Tuesday 7th September 2010
I got an email at work from our director of public affairs stating that there was an article about the Probatron in the 1st September Autocar magazine. It also said that I need to get in quick as the new edition comes out tomorrow. So I rushed down to the shop and sure enough there was an article on page 19. The photo below shows an edited version (I've taken out the stuff that has nothing to do with the Probatron). Another little claim to fame.
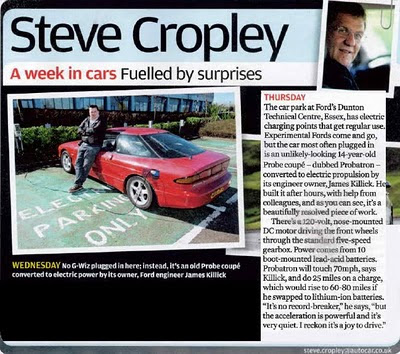
157: Monday 6th September 2010
I have been driving around with my new batteries sliding from side to side for over a week now, so I decided to shift them over to one side and pack the brackets out with wood to stop them moving. There is still scope for a couple of millimetres of movement, but this will be much more secure now and the batteries wont move enough to thump or work the terminal connections lose. I checked all the terminals and the one battery that had moved the most had loosened slightly, but not to be a problem. I tightened them all up a nip and now that problem is solved. Now, back to that current gauge......
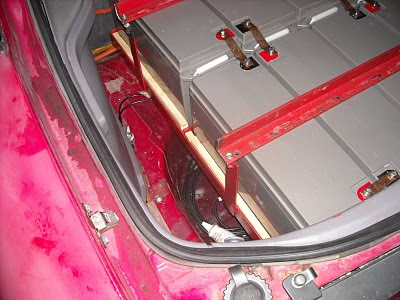
156: Monday 31st August 2010
I have now had the new batteries installed for just over one week and I have had almost no issues. The racks were about an inch too wide and as a result of this, the batteries shift when I go round a corner and this is stressing the hold down brackets. This is easily cured by just pushing the batteries to one side, then packing the bracket out with a piece of wood to stop them from shifting. It is not doing any harm that I can see, but I guess in the long term something is likely to break or wear through, so I shall fix this soon. It is a bit disconcerting when heavy cornering and you get a bump as 400kg of batteries suddenly shift to one side. I shall have to slow down a bit on corners until I have them packed out. The problem with the racks is that they were made using the measurements given by the manufacturer of the batteries and the reality is a few millimeters different, and when you have several batteries in a string, you get the accuracy exaggerated. This is why the racks were too short and too wide. Next time I shall fit the rack to the batteries exactly by laying the whole lot out beforehand. Anyway, some good news, I have achieved 30 miles on a single charge for the first time. I expect this figure will go up in the next few weeks as the batteries become further conditioned and depending on the journeys I do. I am pleased also that this 30 miles was made up of several short, stop-start type journeys, some night driving with lights and after being left over night as well. So this is almost the worst case. I guess that will come with the winter cold and darkness. However, I shall always be able to get to work even if this is completely in the dark with the heater and lights on the whole time with plenty of battery to spare.
155: Sunday 22nd August 2010
I laid the rear battery bracket on the ground and tried 2 batteries in it to make sure they would fit. I had made the total length slightly too short so the handles on the batteries were clashing. I wasn't prepared to remodel the bracket, so a wooden block under one end of one of the batteries allowed the handle to overlap and get the distance I need. Making this change introduces other problems; the electrical connections were no longer lined up and the hold down brackets were too short. To resolve these issues, the copper straps were made with an angled step in them so they can connect at two different levels and I cut the bolts off the hold down bracket and welded new ones on the end with more thread available. This extra work added about an hour.
----
I applied the coat of customary red paint and set about making the copper link straps and cutting the hold down straps to the correct length and drilling them.
----
Unfortunately by extending the bolts for the hold down bracket, the new paint was damaged. I can touch this up another time as this bracket is accessible with all the batteries in the car.
----
With all the bits made, I mounted the rear battery bracket in the trunk, loaded the batteries and connected them. You can see in this photo that 2 batteries just about fit side-by-side in the trunk. There is only about 15mm of space right at the back.
----
As the batteries cover most of the floor of the trunk there was no way I could use the spare wheel well, so this has a new home just to the right of the batteries. I shall make a cover for the new battery layout as the terminals are exposed and I want to be able to use the remaining space for a bit of shopping or whatever. The alternative possibility for the future is to cut the floor out where the fuel tank was and mount the batteries there. I think I will wait until I can get Lithium Iron Sulphate batteries before I make that change.
So now with everything back together I went for a test drive. I was keeping a keen eye on the off-load voltage showing on the motor controller programming unit test function display. I took it down to 116v and had completed 22.5 miles. It still had a good pull even at that level. That's pretty good since the batteries had not been charged since new and judging by the boxes they came in, that was a while ago. Once I got past 15 miles I was smiling as that was my best distance for quite a long time with the old batteries before they started to deteriorate.
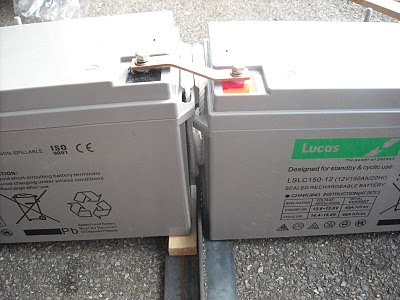
I applied the coat of customary red paint and set about making the copper link straps and cutting the hold down straps to the correct length and drilling them.
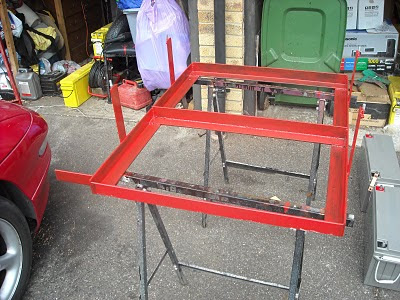
Unfortunately by extending the bolts for the hold down bracket, the new paint was damaged. I can touch this up another time as this bracket is accessible with all the batteries in the car.
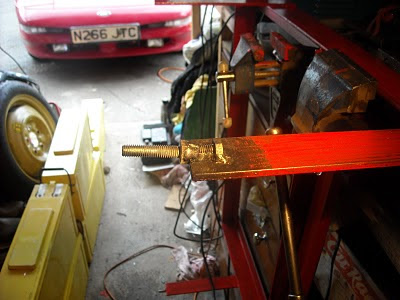
With all the bits made, I mounted the rear battery bracket in the trunk, loaded the batteries and connected them. You can see in this photo that 2 batteries just about fit side-by-side in the trunk. There is only about 15mm of space right at the back.
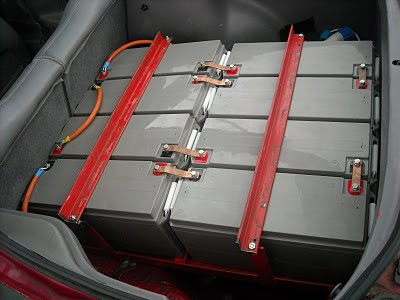
As the batteries cover most of the floor of the trunk there was no way I could use the spare wheel well, so this has a new home just to the right of the batteries. I shall make a cover for the new battery layout as the terminals are exposed and I want to be able to use the remaining space for a bit of shopping or whatever. The alternative possibility for the future is to cut the floor out where the fuel tank was and mount the batteries there. I think I will wait until I can get Lithium Iron Sulphate batteries before I make that change.
154: Saturday 21st August 2010
I had to make one more cut before I could assemble the base of the rear battery rack, but first I was out to the shops to buy some welding rods. I took the old hold down strap and cut it down to fit the width. I then welded the rack together and tried it in the trunk. It seems to fit well and did not need to be raised as the spare wheel cannot sit in it's well any more. I then measured up for an outrigger for the bottom left fixing point as the corner of the rack was in mid air above the spare wheel well.
----
In the photo below (taken from the side) you can see the outrigger added. I made this from angle iron and welded it in as many places as possible as it will be providing support and not just positioning the batteries. I drilled holes in the bracket at the top to fit the existing fixing from the last bracket, then fitted the bolts and drilled holes for the bottom end so I had marks to fit riv nuts to the body. I installed these then the whole bracket was secure.
----
The next step was to make the brackets for the hold downs to go across the top. I had given the last of my threaded stud to one of my neighbours so he could fit a chrome bull bar on the front of his van, so I had to shave the heads off four 8mm bolts and weld them to the brackets made from flat steel bar. In the photo below you can see the hold down brackets added. We were going to a torchlight parade in Southend so I had to pack up and get ready to go out. I could have used another hour just to get some paint on ready for tomorrow so I could go straight to fitting the batteries, but it was not to be. First job tomorrow painting, then to make up the 2 hold down straps.
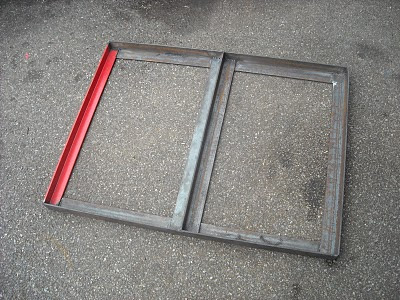
In the photo below (taken from the side) you can see the outrigger added. I made this from angle iron and welded it in as many places as possible as it will be providing support and not just positioning the batteries. I drilled holes in the bracket at the top to fit the existing fixing from the last bracket, then fitted the bolts and drilled holes for the bottom end so I had marks to fit riv nuts to the body. I installed these then the whole bracket was secure.
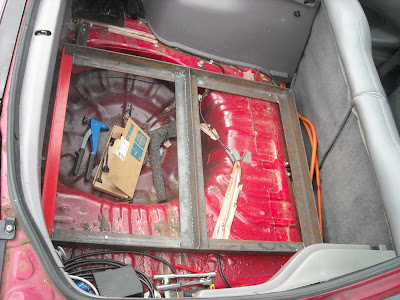
The next step was to make the brackets for the hold downs to go across the top. I had given the last of my threaded stud to one of my neighbours so he could fit a chrome bull bar on the front of his van, so I had to shave the heads off four 8mm bolts and weld them to the brackets made from flat steel bar. In the photo below you can see the hold down brackets added. We were going to a torchlight parade in Southend so I had to pack up and get ready to go out. I could have used another hour just to get some paint on ready for tomorrow so I could go straight to fitting the batteries, but it was not to be. First job tomorrow painting, then to make up the 2 hold down straps.
153: Friday 20th August 2010
I fitted the battery hold down bracket and this went in easily without any further modification. I found the 12v charger wedged nicely under the slam panel and that was about where it was before. I then made up a link cable to join the batteries in series.
----
I then moved the DC-DC converter to several positions and found a bracket holding the 2 fan relays that are no longer used. I clamped this up on the bracket sticking out from the bottom of the DC-DC converter and now it is held in it's new position next to the suspension.
----
I then went to the back of the car and took out the old batteries and the rack and started making a new rack. When I was taking the batteries out I found the offending battery had a big bubble on the plastic at the back. A quick run over with my tester revealed a voltage of 10.3v and the others were all 12.3v, so the others may still be serviceable if anybody wants to buy them I have 9. I decided to change the layout again to improve the connections and keep them to copper straps and really short. I want to avoid making up cables as much as possible. There is much less to go wrong with a simple copper strap. So looking into the trunk the layout will be 2 rows of 4 batteries. For this I only need to make one link cable and the rest can be joined with copper straps. It also looks a lot neater. I got most of the metal cut, but ran out of welding rods, so I packed up for the night. Tomorrow I can finish cutting the pieces and welding them all together, then I can paint it. When the paint is dry I can install the bracket, load the batteries and connect them, then I should be mobile again.
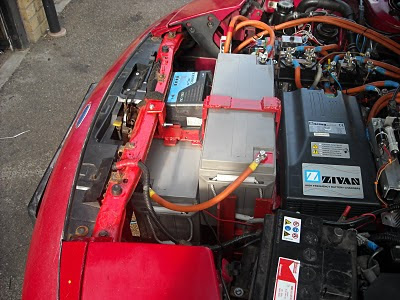
I then moved the DC-DC converter to several positions and found a bracket holding the 2 fan relays that are no longer used. I clamped this up on the bracket sticking out from the bottom of the DC-DC converter and now it is held in it's new position next to the suspension.
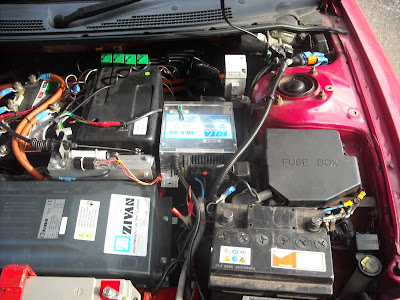
I then went to the back of the car and took out the old batteries and the rack and started making a new rack. When I was taking the batteries out I found the offending battery had a big bubble on the plastic at the back. A quick run over with my tester revealed a voltage of 10.3v and the others were all 12.3v, so the others may still be serviceable if anybody wants to buy them I have 9. I decided to change the layout again to improve the connections and keep them to copper straps and really short. I want to avoid making up cables as much as possible. There is much less to go wrong with a simple copper strap. So looking into the trunk the layout will be 2 rows of 4 batteries. For this I only need to make one link cable and the rest can be joined with copper straps. It also looks a lot neater. I got most of the metal cut, but ran out of welding rods, so I packed up for the night. Tomorrow I can finish cutting the pieces and welding them all together, then I can paint it. When the paint is dry I can install the bracket, load the batteries and connect them, then I should be mobile again.
152: Thursday 19th August 2010
Yesterday I spent most of my spare time putting the battery rack back in the front of the car and remounting all the other stuff that I had to remove to get it out. I put the 2 batteries in the rack and connected them. I had to make some stops on the bottom of the rack for the bottom battery to sit up against. For this I just cut off a small piece of angle iron, drilled and bolted it to the bottom of the battery rack. I took the old hold down bracket and cut it to modify it to the new batteries. This was much easier than starting a new bracket, so I had to make one part shorter and the other part longer to fit the new batteries that are wider than the old ones. Today I got to remaking the bracket to the correct size for the new batteries. I had some steel bar that I cut to extend the bracket, then welded it all back together. In the photo below you can see the modified bracket all freshly painted with fire engine red Hammerite. This is now ready to go back on when the paint is dry. I need to make a cable to link up the 2 batteries and remount the DC-DC converter and 12v battery charger as they were on top of the old batteries, then the front end is all done. My friend dropped off some more angle iron as well for the back end brackets, so I am all set to start on this tomorrow. I have an early finish at work tomorrow (P.O.E.T.S. day), so I should get a fair amount done and hopefully I will be back on the road some time over the weekend.
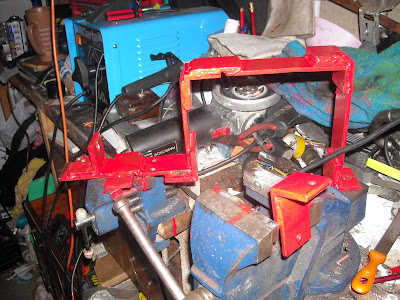
151: Tuesday 17th August 2010
Monday the new batteries arrived as planned. They are actually Lucas batteries and Numax is another brand name. I sort of knew this, but these are clearly marked Lucas. The spec is what I expected. They are 44kg each and that is about the same as the ones I am taking out. The dimensions are such that I can only get 2 in the front of the car and that means I need to put 8 in the trunk. This required a quick remodel of the layout on the PC, printed it off and set about refitting them. I didn't get much done yesterday as I was busy trying to bodge the batteries in, then having a hissy fit about the mess in the garage. Once I had calmed down I decided this is not the right approach as everything else so far has been done with consideration and very little bodging. I decided to just remove the front battery rack and cut it down to the right size for the new batteries.
----
You can see in the photo below that the bracket had to be adjusted about 80mm narrower to be able to sit the batteries on the rack. I used my angle grinder to remove the bracket, then I drilled a hole through the bracket parts and cleaned up all the ends with a file and finally bolted it together. Then into the garage for more of my spectacular welding :-). Now the bracket is sitting in my vice with a fresh coat of that fire engine red Hammerite paint on the exposed parts where I have made alterations.
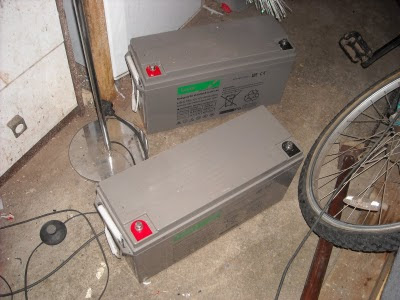
You can see in the photo below that the bracket had to be adjusted about 80mm narrower to be able to sit the batteries on the rack. I used my angle grinder to remove the bracket, then I drilled a hole through the bracket parts and cleaned up all the ends with a file and finally bolted it together. Then into the garage for more of my spectacular welding :-). Now the bracket is sitting in my vice with a fresh coat of that fire engine red Hammerite paint on the exposed parts where I have made alterations.
150: Friday 13th August 2010
Last week the batteries gave out on the Probatron. I was driving along on a local journey, and after about 3 miles the batteries let out a scream, a sulphurous egg smell and I had a drastic loss of power causing the controller to reset. I guess this is what happens when a battery reverses. I have heard of this phenomenon, but never experienced it. Fortunately this happened when I was on my way back and I only had to go round a corner then park up. So now getting some new batteries has moved up the agenda somewhat. First I needed to find funding as I had already worked out what to get and where to get them from. I eventually figured out how to pay and made the order yesterday. I got a phone call today saying that the batteries had arrived at the depot and they will get them out to me on Monday. The batteries I have ordered are Numax SLC150-12 AGM lead acid batteries, 10 of. They are 12v each and 150Ah @ 20 hrs. I now need to rebuild the battery racks as these are different dimensions to the previous batteries.
149: Tuesday 3rd August 2010
Not much happening at the moment. I went to build the circuit for the current sensor and I looked at the data sheet and found that I need 3 capacitors and a regulated 5v supply. I had none of these parts, so I ordered them on-line today and they should arrive before Friday I ordered a 7805 voltage regulator as this is a fairly standard 5v regulator. I am on vacation at home at the moment and I am doing some building work on the back of my house, so progress on the Probatron is slow. I am also trying to figure out how to raise some money for a new set of Lead acid AGM batteries. I have some lined up from a supplier. They are Numax 150Ah AGM batteries and will cost around £1868 for 10 batteries. I prefer Lead acid AGM because they are relatively cheap, but the AGM construction is sealed and built for taking regular heavy loads and recharging. These are the best for their regen ability as "opportunity charging" is not a problem.
148: Friday 23rd July 2010
Last weekend I managed to find some time to mount the 9 blue ultra-bright LEDs behind the numbers of the rev counter in my instrument cluster for the instantaneous amps x 100 bargraph display. I also reworked the LEDs in the state-of-charge gauge that I have mounted behind the fuel gauge mask. It now has 4 red, 1 blue, then 5 green indicators. It seems to work o.k. now after a little bit of tweaking. When the indicators are red then the car will be running slower and I need to get it on charge. Now with 10 LEDs I can tell much easier when that time is approaching. It still drops down when I am driving, but when I release the throttle pedal I can get a good reading. I am not going to fix this quirk as when I have my matrix display working, it will just be rough guide. The photo below shows the 9 blue LEDs mounted.
----
The next photo shows the ribbon cable connected. I used the same connector strip as the state-of-charge gauge, so to give it a quick test I swapped them over and the blue LEDs light up nicely. I shall post another photo when I have built up the sensor circuit and bar graph driver for this display. I checked the data sheet for the hall effect current sensor and it needs a 5v regulated power supply, so that is another little circuit I need to build. Progress will be slow but steady now as time and money are at a premium.

The next photo shows the ribbon cable connected. I used the same connector strip as the state-of-charge gauge, so to give it a quick test I swapped them over and the blue LEDs light up nicely. I shall post another photo when I have built up the sensor circuit and bar graph driver for this display. I checked the data sheet for the hall effect current sensor and it needs a 5v regulated power supply, so that is another little circuit I need to build. Progress will be slow but steady now as time and money are at a premium.
147: Thursday 15th July 2010
Yesterday we had the Ford vehicle enthusiasts day at the research and engineering centre where I work. There were lots of cars brought in by the employees and I got an award and trophy for best in the Green class. That was unexpected as I did not know they had a Green class. It was nice to be recognised for the hard work. I have all the LEDs to finish up the instruments, then I can remove the motor controller programming unit. I have some reworking to do for the state of charge display as the bar graph driver is working from the general 12v supply and seems to read a lower level on hot days. I shall rewire this to the constant 6v supply that was originally for the fuel gauge, rework the LEDs to 4 red, 1 blue and 5 green, and recalibrate it to work with the 6v supply. This only involves adjusting the multi-turn potentiometer screw until I get sensible readings. Then I shall build up the Amps gauge. I have made a board layout for the circuit, I need to build the circuit and mount the 9 ultra-bright blue LEDs behind the numbers of the rev counter and then fix the current hall effect sensor on the main battery cable to the motor controller, a little bit of calibrating and that will be ready too. Next job after this is the graphic display and I have a new design now. I have been researching the parts to make this display and have to thank Gordon Stalling for his dialogue and circuits etc. I hope this display will be the next evolution of Gordon's design, but one of the big considerations has been cost and I should have it all built for under £50. It won't look cheap though.
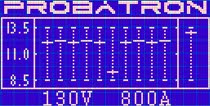
146: Friday 4th June 2010
I looked into the function of the power steering auxiliary contact on the motor controller. There were 2 connectors labelled as auxiliary outputs, one was a supply for a speed control potentiometer and the other was a 120v output for controlling a contactor. Unfortunately the Probatron has a 12v electric power steering system, so this cannot be used directly. I went on eBay and found a relay with 120v coil and had it sent to me. I wired the the contacts of this relay in series with the other control line for the power steering relay and now the steering pump switches off when the motor is not turning. This on it's own is not sufficient as every time you come to a standstill then the steering goes tight, but fortunately the controller has a programmable delay timer built in, so you can set the time delay after the motor comes to rest and before the output switches off. I tried a few different settings and ended up on level 3 (5 seconds). So now when I come to a stop, 5 seconds later the power steering pump switches off. I found that I noticed it was switching off just at the point where I would normally think about switching it off myself using the flip switch, and sometimes earlier. Good thing is I don't have to remember now and when stuck in traffic ques I won't get the power drain of the pump running continuously.
Labels:electric car,ev,nissan leaf,chevy volt
battery car,
battery vehicle,
bev,
electric car,
electric car conversion,
Electric conversion,
electric ford probe,
electric vehicle,
EV,
james killick
145: Saturday 29th May 2010
Today I went back to the electrical wholesaler and got the correct circuit breaker for my fuse board. I fitted it and run the cable through the garage to the new 16A socket just out side my garage door. I now have a dedicated charging point and no more blowing fuses. My wife was asleep, so I told the dogs (Sasha and Merlin) but they didn't care much. See the photo below for the charge point.
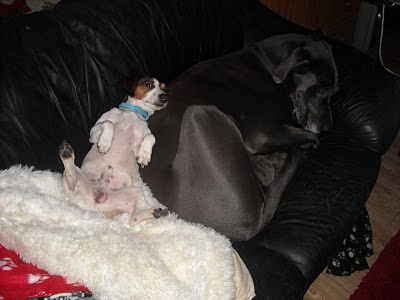
144: Friday 28th May 2010
If you work at Ford in the UK, see if you can still get hold of a copy of the May Ford news. If you click on the article below, you can read it properly.
----
After a succession of blown fuses, I decided it was time to uprate the protection for the charger. It was blowing a 13A fuse about once every week or two, so it must be just borderline. The last time I noticed the plug on my extension lead, the plastic on the live pin had gone all crispy and it fell apart in my hand. I put a new plug on it and moved it to another socket. I bought the parts to wire a 16A socket to my fuse board, but I got the wrong type of circuit breaker for the fuse board that I have. I still had the right parts for the car, so I set about fitting those. You can see in the photo below there is a circuit breaker in the box that mounted on the bracket where the cruise control module used to sit. I removed the cruise control module and the cable (that was always in the way), and mounted the new circuit breaker. It is now rated to 16A just like the caravan type connector. I shall pop down the electrical wholesalers tomorrow morning before my daughter's football training and get the other circuit breaker changed for the right type. I am using a 20A breaker in the fuse board to ensure that it will trip on the car first unless there is a problem with the cable getting cut then it will trip on the fuse board.
After a succession of blown fuses, I decided it was time to uprate the protection for the charger. It was blowing a 13A fuse about once every week or two, so it must be just borderline. The last time I noticed the plug on my extension lead, the plastic on the live pin had gone all crispy and it fell apart in my hand. I put a new plug on it and moved it to another socket. I bought the parts to wire a 16A socket to my fuse board, but I got the wrong type of circuit breaker for the fuse board that I have. I still had the right parts for the car, so I set about fitting those. You can see in the photo below there is a circuit breaker in the box that mounted on the bracket where the cruise control module used to sit. I removed the cruise control module and the cable (that was always in the way), and mounted the new circuit breaker. It is now rated to 16A just like the caravan type connector. I shall pop down the electrical wholesalers tomorrow morning before my daughter's football training and get the other circuit breaker changed for the right type. I am using a 20A breaker in the fuse board to ensure that it will trip on the car first unless there is a problem with the cable getting cut then it will trip on the fuse board.
143: Thursday 6th May 2010
You may remember I had mentioned that the mileage counter was not working and I now know how important this is. I had a disaster on the way to work. My wife had asked me to drop off some paperwork on my way in, so I set out with the paperwork and arrived at work and it was still on the passenger seat, damn! I had gone to work in sport mode as it is only 7 miles and this is easy, but now I had to go part way back and return to work. Without the mileage counter I had no idea how far I had gone and I thought it was only an extra 2 miles, but it turned out to be about 11 miles extra round trip. I got within 1 mile of my work and could go no further without going really slow and damaging the batteries. So I had to get a tow for the last mile. I did stick it in 5th gear and let the regen charging put some back while I was being towed. I had to wait about 30 minutes for rescue and ended up about an hour late for work. I had originally arrived early. I now appreciate how important the mileage indicator is and when I got home from work I set about fixing the counter. I stripped the instrument cluster out of the car and took the counter mechanism apart. When I was drilling the holes for the LEDs on the back of the fuel gauge markings, a tiny piece of the plastic swarf had gone in the cogs and jammed them. I gave it a quick blow, put it back together and it is all working again now. No more range anxiety! Next job is to build a bar graph driver circuit for the 'motor amps' meter LEDs, get the LEDS and mount them. Until then I have the rectangular LED bar graph matrix that I used for the temporary fuel gauge to get started with.
142: Wednesday 5th May 2010
I finished up the charge indicator LEDs. When I was trying to find a supply for the connection to the common terminals on the 120v battery charger, I picked up a 12v supply from the diagnostic connector. While I was making the connections, the other end of the wire touched a screw head and the horn went off continuously. So I got a piggy-back connector on the fuse block for the control box and looped across to a spare fuse slot instead and fitted a 5A fuse in it. Then I picked up the other side of the fuse to the common terminals. I wired the normally open contacts for aux1 and aux2 on the charger to the LEDs. I had already installed 1k drop resistors at the LED ends. Now when I plug the charger in the bottom blue LED comes on (see photo), and when the charge is complete both LEDs come on. If the fuse in the mains supply blows or the supply is interrupted for any other reason then all the LEDs are off, simple!
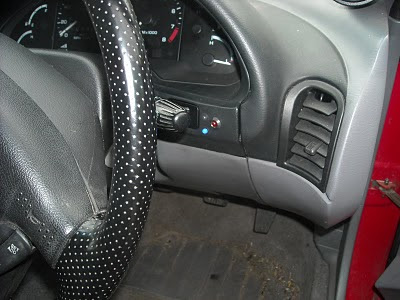
141: Tuesday 4th May 2010
Today I intended on getting my charge indicators working, but the distraction was that one of my external hard drives wouldn't work on my PC, so I spent ages trying to fix it to no avail. I did get the 2 x 5mm blue LEDs mounted on the cluster bezel with the cable and a 3 pin connector on the end. Small progress! Tomorrow I will try and get the wires through to the charger so I can connect it all up. One indicator shows that the mains electric supply is connected and the other shows when the charge is complete. As I have blown a few fuses it will be useful to see when the mains has gone off. While the car is charging, if you listen carefully you can just about hear the fans in the charger. But without opening the hood I have no way of knowing it has completed until now (well maybe tomorrow).
140: Sunday 2nd May
Didn't really do anything today as I was supposed to limit my car projects to weekdays. I was also supposed to be building a brick wall, but it rained nearly all day. I did go for a little drive (providing the Dad taxi service) and the gauge is working fine, and I took some more photos. This time they came out much better due to the day light. The first photo is more like what you see at night and the second like daytime. You can see how weak the yellow and orange LEDs are in these shots. I will be swapping these for red ones and adding 2 more green to the top end of the scale. For some reason the mileage counters have stopped working. It is probably where I took the cluster apart. The speedo still works fine, but I can't tell how far I have gone. It is a good job that I now have a battery level indicator so I know when to go on charge. It still looks much clearer in real life than in the photos.
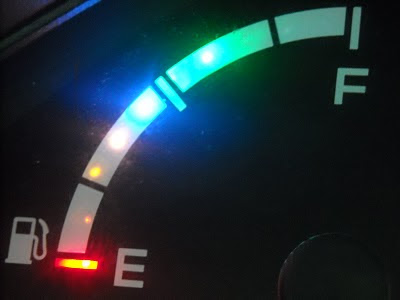
139: Saturday 1st May 2010
I have now completed 1000 miles of electric driving and it has been relatively trouble free.
----
I left the newly glued LEDs to set overnight and then joined all the anodes together with solder. I had soldered a strip of pins onto one end of a ribbon cable that I salvaged from my "computer bits" draw and then stripped the other ends and soldered them to each LED cathode and one wire to the joined up anodes. I then plugged the pin strip into my prototype board, applied the correct resistance and checked they all worked. The orange and yellow ones didn't appear as bright as the red, blue and green. Next I took the LED matrix display off the circuit board and mounted a strip of pin sockets in its place for the ribbon cable to connect to. I gave the circuit a quick test using a potentiometer to provide the input voltage and it worked fine as a curved bar graph on the fuel gauge. Next I put some black tape over the hole where the needle broke off the fuel gauge from when I dropped it. I put insulation tape round the legs of the LEDs and mounted the gauge back into the instrument cluster.
----
I then mounted the cluster back in the car and connected the circuit. A quick test, then I put the rest of the trim back together. In the photo below you can get an idea of how the gauge will look at night. The photo was really difficult to take as in real life you can see definite dots where the LEDs are. All the LEDs look like the top one in the photo.
----
If you click on the photo below you can see what it looked like when I used flash on the camera. This gives and idea about how it would look in daylight, but once again in reality it is a lot clearer than in the photo and perfectly acceptable for normal driving. I am not entirely happy with the orange and yellow LEDs, so I am going to swap them for red when I add the other 2 green LEDs. I am keeping the blue because after a quick drive from a half flat battery pack I found that when the blue LED goes out it starts getting a bit sluggish and really needs to go back on charge. I checked the tester on the programmer and this was at about 119v, so that rings true.
So after several weeks experimenting I now have a separate "state of charge" gauge that shows when I lift off the throttle. This is a quirk I am prepared to suffer. I might come back to this at a later date as I am planning a battery monitor for each of the 10 batteries using a text display showing a bar graph for each battery, then I could use the PIC chip to sample the overall voltage when the throttle is released, keep the display showing this level and update it when the throttle is released again, so the gauge will show a steady display. I will consider this a future upgrade. Next is the Ammeter. I just need to order 10 ultra bright 5mm blue LEDs for this then I have all the bits to get it working. I think I will make a start and have the matrix display that I used before until I get the proper LEDs. This time I will have it hanging down by the cluster as hanging out of the air vent was not easy to see.
----
I left the newly glued LEDs to set overnight and then joined all the anodes together with solder. I had soldered a strip of pins onto one end of a ribbon cable that I salvaged from my "computer bits" draw and then stripped the other ends and soldered them to each LED cathode and one wire to the joined up anodes. I then plugged the pin strip into my prototype board, applied the correct resistance and checked they all worked. The orange and yellow ones didn't appear as bright as the red, blue and green. Next I took the LED matrix display off the circuit board and mounted a strip of pin sockets in its place for the ribbon cable to connect to. I gave the circuit a quick test using a potentiometer to provide the input voltage and it worked fine as a curved bar graph on the fuel gauge. Next I put some black tape over the hole where the needle broke off the fuel gauge from when I dropped it. I put insulation tape round the legs of the LEDs and mounted the gauge back into the instrument cluster.
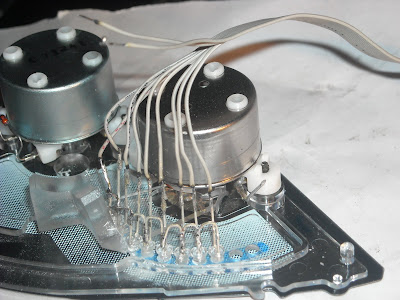
I then mounted the cluster back in the car and connected the circuit. A quick test, then I put the rest of the trim back together. In the photo below you can get an idea of how the gauge will look at night. The photo was really difficult to take as in real life you can see definite dots where the LEDs are. All the LEDs look like the top one in the photo.
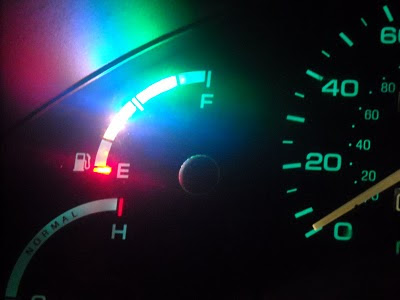
If you click on the photo below you can see what it looked like when I used flash on the camera. This gives and idea about how it would look in daylight, but once again in reality it is a lot clearer than in the photo and perfectly acceptable for normal driving. I am not entirely happy with the orange and yellow LEDs, so I am going to swap them for red when I add the other 2 green LEDs. I am keeping the blue because after a quick drive from a half flat battery pack I found that when the blue LED goes out it starts getting a bit sluggish and really needs to go back on charge. I checked the tester on the programmer and this was at about 119v, so that rings true.
So after several weeks experimenting I now have a separate "state of charge" gauge that shows when I lift off the throttle. This is a quirk I am prepared to suffer. I might come back to this at a later date as I am planning a battery monitor for each of the 10 batteries using a text display showing a bar graph for each battery, then I could use the PIC chip to sample the overall voltage when the throttle is released, keep the display showing this level and update it when the throttle is released again, so the gauge will show a steady display. I will consider this a future upgrade. Next is the Ammeter. I just need to order 10 ultra bright 5mm blue LEDs for this then I have all the bits to get it working. I think I will make a start and have the matrix display that I used before until I get the proper LEDs. This time I will have it hanging down by the cluster as hanging out of the air vent was not easy to see.
138: Friday 30th April 2010
I got home from work and stripped the instrument cluster from the Probatron. I had 10 x 5mm blue LEDs and was planning to mount them behind the mask for the rev counter to show the instantaneous Amps (x100). I had been to the electronics store on my way home and asked what they had for 3mm red, yellow and green LEDs, but someone had been in and bought just about all of their stock. So with the task of lighting up the ammeter in hand, I drilled the holes in the plastic behind the mask in line with the numbers on the dial. I put a 5mm blue LED in my prototype board to light it and held the dial over it. I found that didn't shine through as bright, so I went back to the electronics store to get ultra bright LEDs. They didn't have any ultra bright 5mm blue LEDs, so I came away with 3mm ultra bright LEDs in the following colours; 1 x red, 2 x orange, 2 x yellow and 5 x green, making 10 in total, all for the fuel gauge conversion. In the photo below you can see the holes drilled in the plastic behind the fuel gauge mask. I had drawn the blue line where the stripe was and by the application of trigonometry I worked out how far apart they needed to be around the circumference and using my vernier calipers I put scratch marks where I needed to drill.
I then set about mounting the LEDs in the holes. I tested each one before fitting it to be sure. In the first hole went the red LED, then the first orange, but the next hole was by thinner plastic, so when I put the super glue on, it kept falling over. I went to get my pliers so I put a sticky foam pad on the legs of the other LEDs to hold this one, I got the LED legs in my pliers and went to put it in then dropped it on the floor. After 20 minutes on my hands and knees sifting through swarf an dust and scraps of wire and metal etc. I abandoned my search and decided to proceed with 9 LEDs. I put the 2 yellow LEDs in with great care. When it came to the 5 green LEDs I thought I would test them all first, wise move! I found one was blue and one did not work at all. So I decided to mount the blue one next followed by 3 greens. In the photo below, you can see all the LEDs mounted and 2 spare holes that I will come back to another day. I was happyish to settle for 8 LEDs for now. It was better then having a project box hanging out of my air vent. So now I can't tell when it is fully charged properly, but I am more interested in when it is getting low than when it is full right up. My super glue was past its sell by date, so it took a while to set. It would have been a lot easier with fresh super glue. In case of global understanding, super glue is cyanoacrylate glue. I know there are several names for this, but in the UK it is best known as super glue.
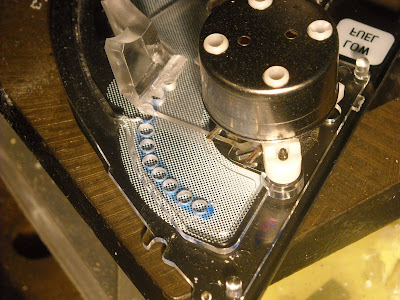
137: Friday 23rd April 2010
I have nearly completed 900 miles since 9th March, so far no real problems with the drive. I am still waiting for the LEDs that I ordered so I set about fixing a typical Ford Probe problem. When I unlock from the drivers door, the passenger door does not unlock and the alarm goes off. This suggests that it is unlocking mechanically, but the switch is not detecting the key so it is not operating the central locking. I took off the door pad and sure enough there was the switch hanging down inside the door. I clipped it back on and now the locks work fine. I put the door pad back together and that is a niggly job out the way. I won't need to go to passenger door now every time I get in the car. Of course now I won't keep setting off my alarm when I forget too. I am looking forward to getting my LEDs so I can get the fuel gauge working now.
136: Sunday 18th April 2010
I mounted the fuel gauge circuit on the back of the cluster, but the gauge did not work. I tried all sorts of different configurations and the problem was due to the gauge mode of operation where it measures a low resistance to ground from the fuel sender originally, so the voltages were arbitrary. In order to make this work I needed a PNP power transistor configure as emitter follower from the output of the circuit. Then disaster struck, I was taking the gauge from the cluster and I dropped it and broke the needle shaft. There was no way to repair it, so I needed a new plan.
----
I thought about just getting another cluster, but decided to use the fascia and mount 10 LEDs around the edge to make it a curved bar graph display. That will look much cooler too and be easy to read. I will have 4 red LEDs at the bottom end, then 3 yellow and 3 green. I went to my local electronics shop and bought an LM3914 bar graph display driver, but they did not have the LEDs I wanted. I have ordered them on-line and now have to wait for them to arrive. I already had an LED bar graph matrix of 10 LEDs in a rectangle mount, so I built the circuit on a prototype board and tested it. That worked o.k. so I then made it up on some strip board and mounted it in the box that I had for the old circuit. I have threaded this through the centre console and calibrated it to show the right number of LEDs for the state of charge. I have a 1000 micro-Farad capacitor on the 120V supply that keeps the voltage when the throttle is pressed, and recharges when the throttle is released. The level does drop off when driving, but it comes back instantly when the throttle is released, so this is just a quirk that I will have to get used to. Anyway the temporary set-up is now in use and working well, so when the LEDs arrive I can work on mounting this all in the cluster. It is difficult to make out the LEDs in the photo, but they are there in the white rectangle in the black box hanging out of the centre console in the photo below. All 10 LEDs are "on"as I had just charged up the batteries and the display on the programmer is reading 132.3 volts. I have temporarily mounted the programmer unit on my Tom-Tom bracket on the air vents as it was getting in the way down by the gear lever. Fortunately it flips up so I can still adjust the volume on my stereo.
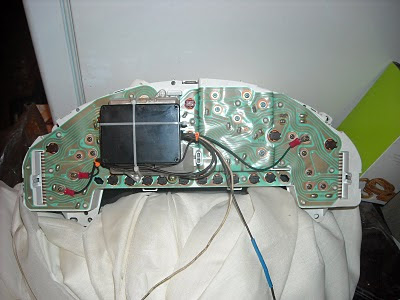
I thought about just getting another cluster, but decided to use the fascia and mount 10 LEDs around the edge to make it a curved bar graph display. That will look much cooler too and be easy to read. I will have 4 red LEDs at the bottom end, then 3 yellow and 3 green. I went to my local electronics shop and bought an LM3914 bar graph display driver, but they did not have the LEDs I wanted. I have ordered them on-line and now have to wait for them to arrive. I already had an LED bar graph matrix of 10 LEDs in a rectangle mount, so I built the circuit on a prototype board and tested it. That worked o.k. so I then made it up on some strip board and mounted it in the box that I had for the old circuit. I have threaded this through the centre console and calibrated it to show the right number of LEDs for the state of charge. I have a 1000 micro-Farad capacitor on the 120V supply that keeps the voltage when the throttle is pressed, and recharges when the throttle is released. The level does drop off when driving, but it comes back instantly when the throttle is released, so this is just a quirk that I will have to get used to. Anyway the temporary set-up is now in use and working well, so when the LEDs arrive I can work on mounting this all in the cluster. It is difficult to make out the LEDs in the photo, but they are there in the white rectangle in the black box hanging out of the centre console in the photo below. All 10 LEDs are "on"as I had just charged up the batteries and the display on the programmer is reading 132.3 volts. I have temporarily mounted the programmer unit on my Tom-Tom bracket on the air vents as it was getting in the way down by the gear lever. Fortunately it flips up so I can still adjust the volume on my stereo.
135: Sunday 11th April 2010
Thursday I had an interview with Ford News about the Probatron. We chatted about the electric driving experience, had some photos done and then I sent them an email with the features of the car. That was cool. Last week I designed the circuits for the fuel gauge and rev counter conversion to state of charge and ammeter respectively. I then ordered the parts I needed from an electronics supplier. Today I constructed the 2 parts of the circuit for the fuel gauge to state of charge gauge conversion. The first part shown below takes 135v to 115v range and strips off 110v with zener diodes making the result between 25v and 5v. This goes through a potential divider to further reduce the voltage to a signal to drive the LED in an opto coupler. Typically opto couplers are used to separate different voltages, but only for on and off signals. I am using it for a linear signal. I tested it on a prototype board and it works fine. This way the 120v system and the gauge are isolated by the opto coupler. I only had one project box so I designed this circuit carefully so that it fits in a marker pen case. This will make it easy to mount on the throttle linkage bracket and it will be hidden.
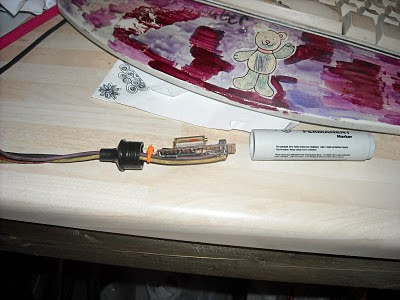
----
The second part of the circuit picks up the signal from the LED in the opto coupler using the photo-transistor inside the opto coupler. This is configured as an emitter follower that feeds a transistor inverting amplifier. This then flips the voltage. The amplifier supply is provided by a 3.6v zener diode and a normal diode making the voltage 3.2v on the supply through a resistor to the collector of the power transistor. The output will measure 3.2v when the input is 113volts. It will measure 2.7v when the input is 116volts and it will measure 0v when the input is between 128 and 135volts. The gauge shows empty when it is supplied with 2.7v and full at 0v. So this will tell me empty at 116v and that is about 20% remaining and that is as low as I would want to go with Lead Acid batteries. The input circuit is adjustable, so when I get Lithium batteries then I can pop the circuit out of the marker pen case, adjust it then pop it back in.
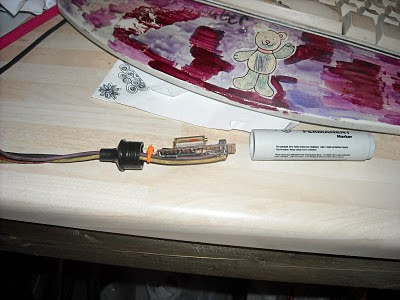
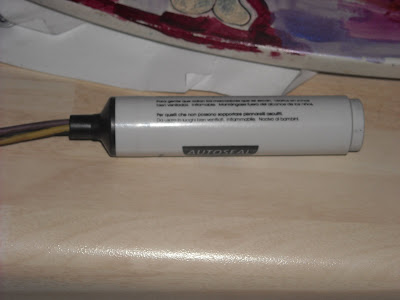
The second part of the circuit picks up the signal from the LED in the opto coupler using the photo-transistor inside the opto coupler. This is configured as an emitter follower that feeds a transistor inverting amplifier. This then flips the voltage. The amplifier supply is provided by a 3.6v zener diode and a normal diode making the voltage 3.2v on the supply through a resistor to the collector of the power transistor. The output will measure 3.2v when the input is 113volts. It will measure 2.7v when the input is 116volts and it will measure 0v when the input is between 128 and 135volts. The gauge shows empty when it is supplied with 2.7v and full at 0v. So this will tell me empty at 116v and that is about 20% remaining and that is as low as I would want to go with Lead Acid batteries. The input circuit is adjustable, so when I get Lithium batteries then I can pop the circuit out of the marker pen case, adjust it then pop it back in.
Tomorrow I hope to get the circuits fitted to the car along with a 1000 micro Farad capacitor to the throttle switch so the the capacitor holds the voltage that is present when the throttle is released only. So this is off-load and should be fairly stable. The gauge itself takes a couple of minutes to stabilize when the readings change anyway. I will monitor the gauge with the zapi programmer tester function showing the instantaneous voltage so I can check it when I stop and get an idea of how it reads for the different voltages. The gauge behaviour wasn't exactly linear. You may feel that the last bit of fuel goes quicker, but it doesn't, just the gauge goes down quicker due to the non-linearity of the gauge. It is not drastic and I am confident the gauge will give me a good indication. At the same time I have not had to add another gauge, but using a redundant one instead. This keeps it all neat looking. As an added bonus, when the gauge gets down a fair way, then the fuel low warning light comes on too, how's that! All the components I have bought for both gauges have come to just over £20 and that is less than half the price of an ugly add-on gauge and not including some kind of pod to put it into as well. I like to have my instruments look like they have always been in the car and not look like a dodgy add-on. I've seen quite a few examples of this on-line. I am not going to label anybody specifically.
134: Monday 29th March 2010
I found out that using the cutback inputs on the motor controller does limit the speed of the motor, but does not make it any more efficient. For this a reduction in current is needed. I also found out that if the brake and throttle inputs are activated at the same time then the current is reduced to 500A maximum. So I got to rewiring the relays. In sport mode when the throttle is pressed you get the full 800A available and it accelerates really well. I have used the relay to provide 120v to the brake input (switches it off), so just the normal disc brakes, and when the throttle is release then this activates cutback 3 that is set to maximum speed limit and reduces the release regen to the minimum level and is cutback. When the throttle is pressed again the cutback is disabled so full beans again. For the economy mode, pressing the throttle activates the throttle and brake inputs together giving reduced current and the speed limit set by cutback 2. releasing the throttle removes the brake input and provides the release regen braking. pressing the brake pedal on its own provides extra brake regen charging. As the motor speed is limited then there is no arcing. There is no arcing in sport mode as there is only a tiny amount of regen. So then the motor can go full speed. During the week I am getting a comfortable 25 miles on a charge in economy mode and 17 miles in sport mode if I take it easy.
That was all done during the week, but the weekend just gone I was finding out some of the characteristics of the gauges. I want to use the old fuel gauge for state of charge and the tacho as the ammeter (x100). The fuel gauge shows exactly at the bottom of the scale (empty) with 2.7 volts on the input and full when the voltage is zero. Now I need to make 114v = 2.7v and 134v = 0v. I have a plan and it will be isolated between the batteries and the gauge itself using an opto isolator. The tacho did not respond to voltage at all. I suspected it would only work from a pulse train, but I tried it all the same just to be sure. Using a simple voltage controlled oscillator a hall effect current sensor and a transistor I can drive the tacho. This will also take some working out, but I will get it working soon enough. Then I will have instantaneous current and state of charge. The state of charge will only be measured when the throttle is released so it is off load.
That was all done during the week, but the weekend just gone I was finding out some of the characteristics of the gauges. I want to use the old fuel gauge for state of charge and the tacho as the ammeter (x100). The fuel gauge shows exactly at the bottom of the scale (empty) with 2.7 volts on the input and full when the voltage is zero. Now I need to make 114v = 2.7v and 134v = 0v. I have a plan and it will be isolated between the batteries and the gauge itself using an opto isolator. The tacho did not respond to voltage at all. I suspected it would only work from a pulse train, but I tried it all the same just to be sure. Using a simple voltage controlled oscillator a hall effect current sensor and a transistor I can drive the tacho. This will also take some working out, but I will get it working soon enough. Then I will have instantaneous current and state of charge. The state of charge will only be measured when the throttle is released so it is off load.
133: Sunday 21st March 2010
All the time I have been doing this electric car conversion I have had a companion that I believe deserves a mention. This fox sits on top of a pile of bricks that I have on our driveway (next job!) and occasionally takes a sip of water from the little pools on the polythene cover. Right on Foxy...
Yesterday I installed some slave relays for the clutch switch, the brake switch and a "sport / economy" selector switch. These are operated by the 12v switches and pass 120v signals to the motor controller. The clutch relay has 2 purposes; it provides a throttle switch input that disables the release regen because the controller believes the throttle is not released and it cuts the feed to the brake relay so brake regen is disabled. The net effect is the clutch pedal when pushed disables all types of regen. This enables me to change gear without any regen going on. I need to look into the arcing problem, but I have a solution. When the cutback reduces the motor voltage, it also reduces the release regen, so if I add another relay to control the sport mode only, then I can use another cutback input for when the throttle is released therefore reducing the regen when the throttle is released in sport mode. As the speed is limited in economy mode I want remove the cutback when the throttle is released to get the full regen effect. Then I have the best of both worlds and no arcing. The photo below shows the "sport / economy" switch mounted in the centre console just behind the gear lever. It looks like it has always been there and I am really pleased about that. Just need to get a label made up for it now. This fits in with my principle of not cluttering the car with switches and buttons etc. that look out of place.
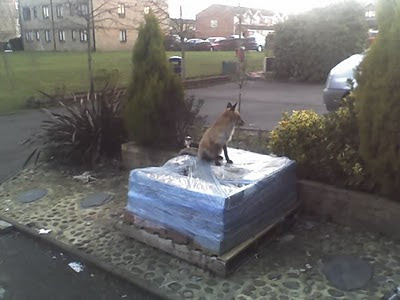
132: Tuesday 16th March 2010
I got 26.6 miles today from a single charge. I have been driving really carefully in 3rd gear only. My next plan to increase mileage is to use the cutback to set up a switch for “sport / economy” so I can limit the throttle amount in economy mode and give it full beans in sport mode. I am also going to rig up some slave relays to my brake and clutch pedal switches so I can introduce the braking regen (loads of charging amps) and disable regen when I touch the clutch pedal. I had it confirmed that the release regen (200A charging) is triggered by the throttle micro switch, so I can use the same feed to the throttle and brake inputs and break the connections with the clutch relay. Then I can select economy mode and use the gears. It will be much easier to maintain a top speed. Also in sport mode I can go through the gears and do some 0-60 runs and find the top speed etc. I am hoping I can borrow the test track at work for this.
I had a disaster this morning, I did not know what had happened for sure until I got home from work, but when I plugged in last night it started charging o.k. When I came out in the morning there was no noise from the fans on the charger so I automatically assumed that the charge was complete. I just about made the 7 mile trip to work and I started worrying about duff batteries and other stuff. I tested the batteries after 90 minutes of charge and everything was fine. Then I remembered that I had a new caravan adapter for the charge lead and assumed that it must have had a 10A fuse in it and the car only got about 1 hr of charge before it blew. When I got home I found that the short extension I had on the end of another extension had blown its fuse and was arcing on the live wire connection. The plug was quite badly burned. So tonight I reversed up the drive so I had plenty of cable and did not need the short extension.
I had a disaster this morning, I did not know what had happened for sure until I got home from work, but when I plugged in last night it started charging o.k. When I came out in the morning there was no noise from the fans on the charger so I automatically assumed that the charge was complete. I just about made the 7 mile trip to work and I started worrying about duff batteries and other stuff. I tested the batteries after 90 minutes of charge and everything was fine. Then I remembered that I had a new caravan adapter for the charge lead and assumed that it must have had a 10A fuse in it and the car only got about 1 hr of charge before it blew. When I got home I found that the short extension I had on the end of another extension had blown its fuse and was arcing on the live wire connection. The plug was quite badly burned. So tonight I reversed up the drive so I had plenty of cable and did not need the short extension.
131: Saturday 13th March 2010
Since I got my tax disc on Tuesday I have had some driving experience now. The batteries seem to have woken up a bit and now I have a confident 18 mile range with some charge still left. I am going to spend some time rigging up the regen through the clutch switch so that it is disabled if I press the clutch pedal at any time. Hopefully this will extend the range a bit further, but definitely give a better feel by providing a bit of "engine braking" and a lump of regen charging when the brake pedal is pressed. There is a choice of levels 0 to 5 for each of "lift-off" regen and brake regen, so I can have a play with these settings and find a good compromise between comfort and regen charge. I also have been in touch with my supplier of the battery discharge indicator as it was showing full when my batteries had run right down. this caught me out one time and I managed to just about trickle home. I found out the gauge was set up for forklift trucks that run for 7 or 8 hours and it only updates once every hour. Since I can flatten my batteries in less than an hour it is next to useless. The supplier is sorting me out with a replacement that shows the instantaneous level. I also need to start making the converter circuits to use the rev counter as an ammeter and the fuel gauge as a charge level indicator. I am currently using the 12v battery gauge as a rough guide to the charge left, but it doesn't change much.
In general I am very happy with the way it drives and today was the first time since Tuesday that I have used my Ford Fiesta. We went to football training that is a 36 mile round trip. I got rid of the old engine off my driveway today also. I have taken off most of the parts that can be sold. I will be making my gauge converter circuit calibrateable, so if you are interested, I can make more. I am also going to make an individual battery monitor display that shows the level of each battery on 10 bargraphs so I can see the state of all the batteries at-a-glance.
In general I am very happy with the way it drives and today was the first time since Tuesday that I have used my Ford Fiesta. We went to football training that is a 36 mile round trip. I got rid of the old engine off my driveway today also. I have taken off most of the parts that can be sold. I will be making my gauge converter circuit calibrateable, so if you are interested, I can make more. I am also going to make an individual battery monitor display that shows the level of each battery on 10 bargraphs so I can see the state of all the batteries at-a-glance.
130: Tuesday 9th March 2010
Today I got my tax disc. It was not without some issues though. First thing I saw when I arrived at the DVLA office was pickets for a strike over pay claims. So I went in and took my ticket. There were only 2 people queing before me. I noticed there was a sign saying that only a limited service would be offered today due to industrial action. My turn came and I handed over my log book, insurance cover note and MOT certificate with the Engineers report. The woman serving me had to fax the Engineers report over to the head office at Swansea. She told me that she was not sure if anybody was picking up faxes at Swansea because of industrial action so it may take a while. I waited a while and I was called up and told that the Engineers report was o.k., but it does not mention the chassis number and this would be needed to process the change of tax class. I got on the phone to the garage and then went there and the Engineer had a signed and stamped report with the chassis number on it, then back to the DVLA. I didn't need to que this time and after a quick check over the new Engineers report I filled in a form for the change of tax class and the log book was changed and then I was issued with the new tax disc. In the photo I have defaced this so it can't be copied. I have blacked out my car registration number and written SAMPLE across it in red. Just below this you will see "NIL" charge and "ELECTRIC" as the class, cool. When I got home I went for a few drives. I only clocked up about 13 miles before the batteries were flat. This is plenty for my commute to work where I can charge up again for the journey home. It is a bit disappointing, but the batteries are second hand and near the end of their life. With a set of nice fresh batteries I should get much more. Anyway, I shall drive it around like this for a while and then try switching on the regen braking to try to recoup some energy back to the batteries.
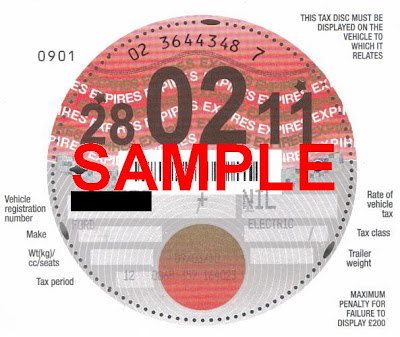
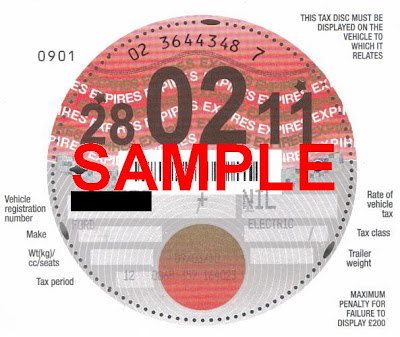
129:Sunday 7th March 2010
Today I wanted to cure the power steering leak. I had a plan and needed to get a 10mm compression coupling from a DIY shop. Football match was a 1:30 kick off for my daughter's team, so that messed the day up quite a bit. They did win 7-0 so that was good. Picked up the coupling on the way to the match. The photo below shows the coupling I had before and you can see at the top between the 2 washers there is a tiny gap and this was where it was leaking from.
----
This photo shows the pump with the Toyota pipe fitted. You can see this does not seal on the casting.
----
I actually got the wrong end of the pipe and it does not seal on a small O Ring, but the fluted end you can see in the photo that seats inside the pump. I cut back some of the plastic coating on the probe pipe very carefully using a heat gun to soften it first so that I did not mark the metal pipe. I measured this and it was exactly 10mm. I did this before I bought the coupling of course!
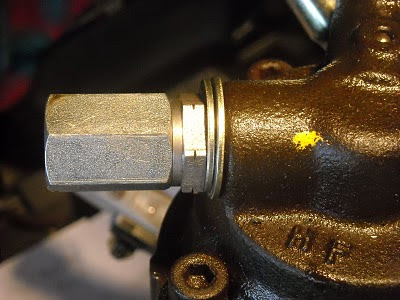
This photo shows the pump with the Toyota pipe fitted. You can see this does not seal on the casting.
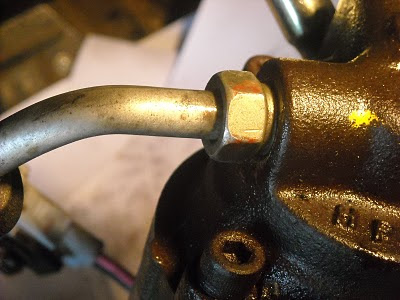
I actually got the wrong end of the pipe and it does not seal on a small O Ring, but the fluted end you can see in the photo that seats inside the pump. I cut back some of the plastic coating on the probe pipe very carefully using a heat gun to soften it first so that I did not mark the metal pipe. I measured this and it was exactly 10mm. I did this before I bought the coupling of course!
I cut the Toyota pipe and joined the coupling to the end of this. I then offered it up on the car to make sure the Probe pipe was in the correct orientation to join on.
----
I then cut the Probe pipe and stripped back the plastic coating. I fitted the coupling on the Probe end. I moved the bracket for the pump mounts as I had to pull the pump up onto it and it was siting at a weird angle in the anti vibration mounts. I was not happy with this so I moved the bracket up and turned it over to put the bracket at the right height for the mounts not to be pulling so much. Then I mounted the pump and connected the pipes together. I ran the pump while putting fluid in the reservoir to get all the air out of the system. A few turns back and forth on the steering got the last of the air out and another top up revealed no leaks hurrah! The Probatron is now truly ready to go for Tuesday when I have the tax disc. I shall put it on charge tomorrow night so it is freshly charged for Tuesday morning when I get back and hopefully it can go out for it's maiden voyage. I will post a short video soon after that.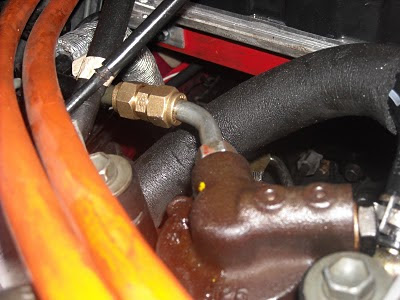
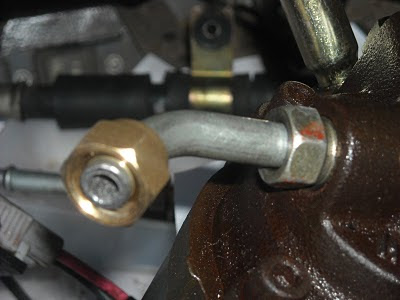
I then cut the Probe pipe and stripped back the plastic coating. I fitted the coupling on the Probe end. I moved the bracket for the pump mounts as I had to pull the pump up onto it and it was siting at a weird angle in the anti vibration mounts. I was not happy with this so I moved the bracket up and turned it over to put the bracket at the right height for the mounts not to be pulling so much. Then I mounted the pump and connected the pipes together. I ran the pump while putting fluid in the reservoir to get all the air out of the system. A few turns back and forth on the steering got the last of the air out and another top up revealed no leaks hurrah! The Probatron is now truly ready to go for Tuesday when I have the tax disc. I shall put it on charge tomorrow night so it is freshly charged for Tuesday morning when I get back and hopefully it can go out for it's maiden voyage. I will post a short video soon after that.
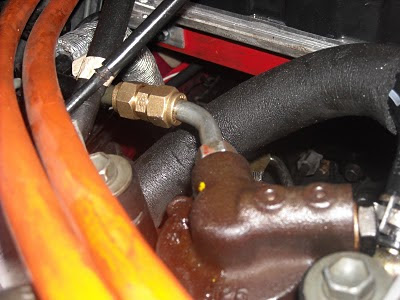
128:Saturday 6th March 2010
Today the weather was good, so after my daughter's football training I cracked on with the paintwork. After yesterday I had done my back in using the polishing machine (heavy) while doing the first T-Cut. Today my wife helped me and we got through the work in double quick time.
----
The first job was to polish with red colourfast T-Cut. My wife was applying the T-Cut and rubbing it in while I was rubbing it off and buffing it.
----
The next job was to apply Autoglym super resin polish. We carried on with the same jobs. I got the best job as I could see the gleam as I was polishing and buffing. The Autoglym really took the shine to another level. In the photo below you can see the "PROBATRON" letters reflecting in the bumper.
----
The next job was to apply the "PROBATRON" letters. This was a crowning moment as I got these from my daughter as a birthday present in December last year. I put them out on a sheet of white paper then measured the whole word. I then worked out how to centre it with respect to the rear centre reflector. I applied a length of electrical tape at the same level as the bottom of the "PROBE 24V" badges and then peeled the back of each letter and carefully stuck them on. Finally I removed the electrical tape.
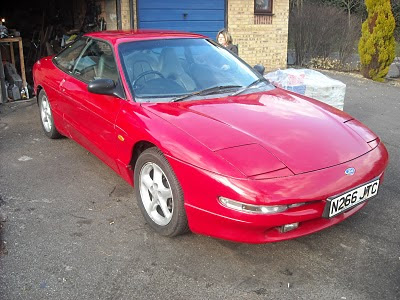
The first job was to polish with red colourfast T-Cut. My wife was applying the T-Cut and rubbing it in while I was rubbing it off and buffing it.
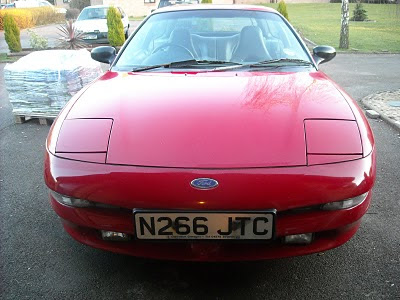
The next job was to apply Autoglym super resin polish. We carried on with the same jobs. I got the best job as I could see the gleam as I was polishing and buffing. The Autoglym really took the shine to another level. In the photo below you can see the "PROBATRON" letters reflecting in the bumper.
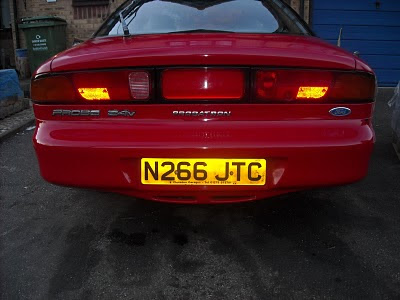
The next job was to apply the "PROBATRON" letters. This was a crowning moment as I got these from my daughter as a birthday present in December last year. I put them out on a sheet of white paper then measured the whole word. I then worked out how to centre it with respect to the rear centre reflector. I applied a length of electrical tape at the same level as the bottom of the "PROBE 24V" badges and then peeled the back of each letter and carefully stuck them on. Finally I removed the electrical tape.
As darkness fell I took another photo then called it a day. I measured the pipes for the Toyota pump and the Probe and both were 10mm. I will go to my local DIY shop tomorrow and pick up a 10mm straight compression coupler so I can cut and join the pipes to give me the correct end for the Toyota pump. That should fix the leak on the power steering pump fitting.
Subscribe to:
Posts (Atom)