No real distractions today, except that it was raining all day. I fashioned a shelter from the outer cover of my old gazebo between the garage door and the car hood. The cardboard is to stop it sinking and getting a pool build up. With a dry (and very cold) working environment I could start.
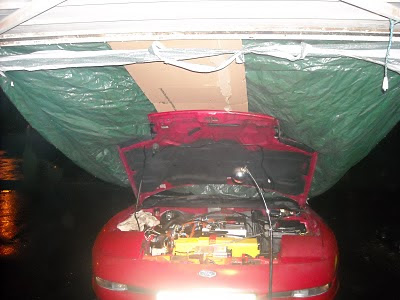
----
I mounted the DC-DC converter onto the battery hold down bracket. I had to make an aluminium bracket to do this so it is nice and secure and doesn't rattle. I need to re-wire the 12v side at some point, but I did not have enough heavy duty cable to do it today, so I used what I had left over from the charger. I also connected up the 12v side of the charger to the contactors, where the battery supply connects.
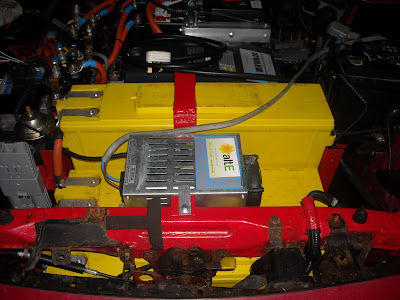
----
I also found a home for the Anderson connectors. I mounted them onto the side of the add-on bracket that I made for the vacuum pump. Of course nothing is so straight forward, initially the location would have clashed with the vacuum pipe, so before I could mount the connectors I had to re-route the vacuum pipes. Fortunately one of the pipes had a nice sharp right angle on it, so that made things simpler. I used riv nuts on the steel angle iron. I found that if I drilled the hole for the riv nut, then drilled into the back with a much bigger drill, but not right through, then the riv nut could spread into the space the bigger drill created. This made it very easy to mount the connectors and as the riv nuts have a small flanged edge, this spaced the connector off of the angle iron. I guess it is about the same as slipping a washer in, but much easier. No fiddly nuts to play with here. I also mounted the three batteries in the front and connected them together. So I am now up to 36v, only another 84v to go. It started getting colder and the rain was coming across so the shelter was only just about keeping everything dry, so I called it a day. I shall make the power connections between the Anderson connector and the contactors tomorrow, then I can move to the back of the car and running the power cables along the underside. Oh and removing the fuel tank of course.
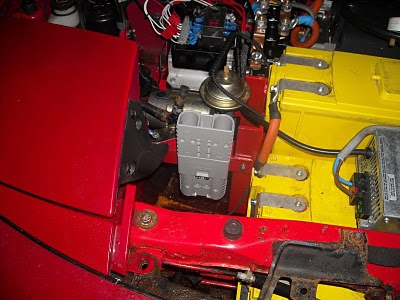